The Importance of Quality Control in Textile Paper Cone Manufacturing
Quality control is a crucial aspect of textile paper cone manufacturing, ensuring that the cones meet the required standards for strength, size, and durability. It plays a pivotal role in minimizing defects and waste in the production process, guaranteeing customer satisfaction, and maintaining the manufacturer’s reputation. The quality of textile paper cones is particularly vital for spinning mills, as these cones serve as essential components in the yarn manufacturing process.
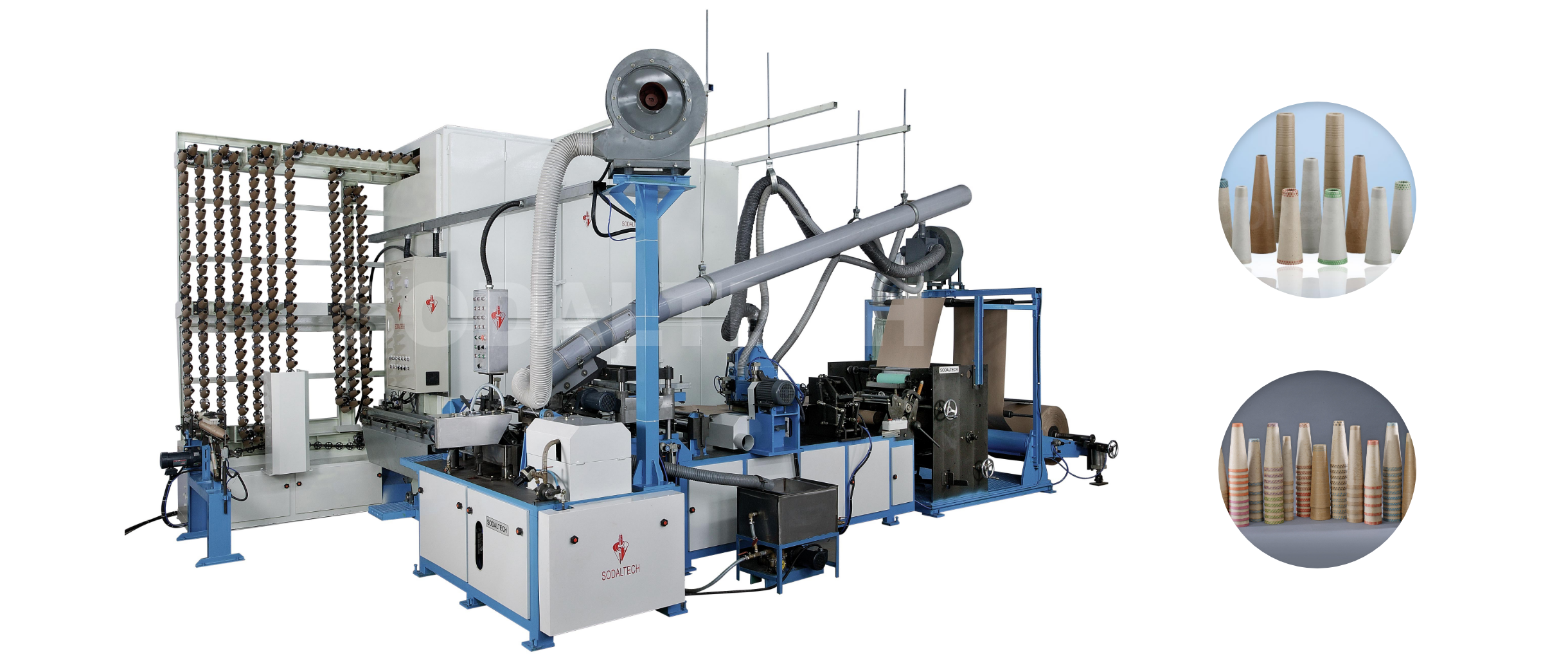
Why Quality Control Matters:
- Quality control ensures that textile paper cones meet customer expectations, fostering higher satisfaction levels and building trust among customers.
- Consistent cone quality reflects positively on the manufacturer’s reputation and minimizes product defects, resulting in improved operational efficiency and reduced waste.
- By adhering to quality standards, manufacturers ensure that paper cones meet required specifications for strength, size, and durability, enhancing overall product reliability and customer satisfaction.
- For spinning mills, the quality of textile paper cones is paramount, as these cones directly impact the efficiency and reliability of the yarn manufacturing process.
Key Steps to Ensure Top-Quality Textile Paper Cones:
a. Raw Material Inspection:
-
- Thorough inspections of incoming paper materials ensure they meet quality standards for strength, thickness, and uniformity, preventing defects in the final product.
- Early detection of problems in raw materials aids in maintaining consistent cone quality and compliance with industry standards.
b. Machine Calibration and Monitoring:
-
- Regular calibration of manufacturing machinery ensures accurate settings for cone size, shape, and winding tension, supporting overall quality control efforts.
- Real-time monitoring systems detect deviations from standard production parameters, enabling immediate adjustments to maintain quality standards.
c.In-process Inspections:
-
- Frequent inspections throughout the manufacturing process identify defects or irregularities in cone formation, allowing prompt resolution to prevent substandard cone production.
- Proper inspection techniques, quality control checkpoints, and documentation ensure consistent cone quality and compliance with standards.
d.Final Product Testing:
- Comprehensive testing of finished cones evaluates their strength, integrity, and dimensional accuracy using standardized testing methods.
- Test results ensure product consistency and reliability, meeting customer expectations and regulatory requirements.
Is Quality Control the Secret to Long-Term Business Success?
- Consistent cone quality enhances customer satisfaction, loyalty, and positive referrals, driving repeat business and reducing costs associated with rework and returns.
- Minimized risk of product recalls, rejections, and returns reduces associated costs and reputational damage, supporting long-term business sustainability and competitiveness.
- Improved operational efficiency optimizes production processes, reduces waste, and maximizes resource utilization, enhancing overall profitability and business success.
Conclusion:
Quality control is the cornerstone of successful textile paper cone manufacturing. By following these essential steps and implementing effective quality control practices, manufacturers can ensure superior cone quality, enhance customer satisfaction, and maintain a competitive edge in the market.
Ready to elevate your paper cone manufacturing process to new heights of quality and efficiency? Contact Sodaltech today and discover how we can help you achieve your goals!